By Bill Giordano
Implementing greenhouses and other covered structures for extending the growing season has been a popular trend in farming’s recent memory. This millennium’s plastic-covered agriculture precedent now spans hundreds of thousands of acres nationally and includes an increase in covered acreage across farms in Maine, when comparing the USDA’s 2017 census data to earlier census years. Trends show no signs of slowing.
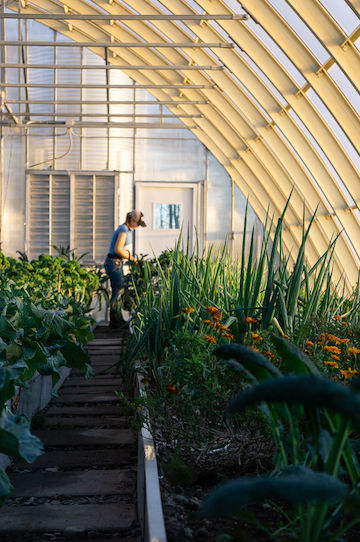
In 2020 the Maine Sustainable Agriculture Society (MESAS) released a report on its Sustainable Year Round Agriculture (SYRA) project, which was designed as a pilot research and demonstration program for novel year-round agriculture infrastructure on commercial farms in Maine. Findings discussed how capital-intensive design systems for covered production infrastructure may not offer a comprehensive pathway to financial sustainability for a majority of producers utilizing covered systems. Rather, it was found that return on investments at the scale that would allow 95% of Maine’s farms to implement covered infrastructure most often come from lower cost alternatives.
Below is a synopsis of different heating systems utilized by two farms in Maine. Additional details, analysis, videos, on-farm interviews and more are available at mesas.org.
Little River Flower Farm
Little River Flower Farm produces certified organic vegetables, cut flowers and pick-your-own blueberries on 10 acres in Buxton, Maine. They utilize over 16,000 square feet of greenhouse space onsite. One of their structures, called “Greenhouse 4,” is a composite arch/polycarbonate glazed greenhouse measuring 45 feet by 144 feet.
Greenhouse 4 was the test site for a trial on heating efficiency using a permeable radiant heated subfloor under raised beds that are used for year-round rotations of cut flowers and leafy greens. The aim of the study was to understand if and how winter and shoulder season crops perform with heat delivered under their root zone, and the costs per square foot of doing so effectively in the farm’s raised bed system.
This “hot” radiant system circulated approximately 150 to 175 degree heat through a hydronic (water-based heat delivery) system using PEX tubing underneath the root zone. The heat radiated up through the root zone and topsoil of the raised beds and into the canopy and ambient air above. The system was originally powered by two 170-BTU pellet furnaces, but was replaced with a 300-BTU Viessmann propane system in 2018.
This system could adequately heat soil for producing vegetables and cut flowers in permanent raised beds. It proved that it could be cost effective commercially when operated by a team of two skilled staff members. At Little River’s scale, it was determined that grossing between $1.50 and $2 per square foot of bed space per month through the winter growing specialty cut flowers or edible leafy greens would offset costs for running the system. Grossing $4 per square foot of bed space would allow a three to six year return on investment on all infrastructure costs. However, this assessment did not consider soil treatments for long-term covered growing (e.g., natural salt accumulation and nitrogen toxicity in covered soils) and assumes greenhouse crops are also grown through a portion of the spring, summer or fall to at least double gross income from a steady winter season of growing. This of course would fluctuate depending on the cost of fuel, as well as the thermal efficiency of the fuel source.
All crops will not perform the same in a radiant soil heating system as they would in a solar- or air-heated system. Certain cold-tolerant crops such as arugula performed poorly in the trial at Little River Flower Farm. However transplanted kale and chard performed well.
The hot radiant heat dried the subsoil and portions of the root zone which created too much temperature fluctuation in the root zone. It also required non-intuitive watering even when the surface was moist. Owner Nancy Stedman and I hypothesized that the thread-like roots certain plants rely on would not do well in the hot root zone system, but we did not analyze root systems or plant biomass in this project.
Little River Flower Farm’s system utilized paver squares as pathways between the raised beds. I hypothesized that heating the pathways, rather than the beds, and covering the bed and paths with a crop blanket just above the canopy would steady the temperature in the root zone while still achieving the desired crop and ambient air heating required to maintain the system. The system we tested was overequipped for the crops in the trials. A cold cropping plan that keeps plants at 38 degrees Fahrenheit, rather than the warm 60-degree target temperature of this trial, would decrease fuel demand and cost significantly.
Anyone utilizing a radiant or ground-heated system in a greenhouse should bear in mind proper depth for an insulated frost barrier. Not doing so will result in heating the ground outside your greenhouse or tunnel instead of within it.
With the advent of low-cost sensor and hardware controller systems, it also would be feasible to design a system that has thermocouples measuring heat in each bed that communicate wirelessly with flow controls at the hydronic system’s manifold to allow a single heat source to reduce or increase temperature on each hydronic loop, thereby affording varying temperatures for different beds.
Taken as a whole, heating the subsoil with a hydronic radiant system can work but those interested should do ample research and tune the system to their needs and be prepared to make changes and learn as you go. Bear in mind that currently this system is still on the expensive side of trials mentioned here, but the costs will likely come down as more is learned about optimizing radiant heat in and under soil.
Six River Farm
Six River Farm, a certified organic vegetable farm in Bowdoinham, Maine, has been expanding their winter production since 2010. They now produce on a few acres every winter in both propane-heated houses and moveable unheated tunnels, double-covering both systems with winter crop blankets on freezing nights.
Co-owner and operator Nate Drummond has invented a crop canopy air duct heater for the propane-heated houses. It utilizes perforated inflatable ducts that remain flat on the ground when the furnace isn’t blowing and delivers heat direct to the canopy when the furnace is active. The whole house is covered in a single crop blanket that provides crops with a 38-degree “livable” temperature for cold-tolerant crops when it is freezing outside. Thermostats are set under the canopy and blanket. Other houses utilize ground-mounted 125-BTU Reznor heaters. Instead of hanging the heater overhead, as is most common, the ground mount allows heat to stay longer where its most needed — under the crop blanket.
The system works very well, with room for improvement. Drummond believes that an electric heating solution is in sight for Six River — preferably a system that can be powered by the farm’s solar array. This, he hopes, would allow their photovoltaic array to power their farm’s heating needs in the winter.
With a decade of winter market expansion under their belt, Six River Farm reflects that despite the heating expenses required for robust winter production, the community impact of maintaining a year-round work force — in the winter of 2021 they employed 12 people — has proven to be a winning strategy for their farm. These local jobs help produce local food for Maine’s expanding year-round produce market.
Heat Technologies Used in Covered Agriculture
Here are a few additional technologies and covered agriculture approaches that could be useful, with a bit more field testing, for Maine growers.
Phase change material (PCM) works like an ice pack that you would put in a cooler, but in reverse; it stores heat when its abundant and releases it at a factory-set phase change temperature. PCM is being tested in end walls, north-facing walls, passive air ducts and even in the walls of raised beds.
Active air exchange ducting may improve the efficacy of a Trombe wall type of solar heater. A ridge vent could recirculate or ventilate the inside air.
Ground battery systems, also referred to as ground to air thermal energy exchangers, pump heat into the ground under the greenhouse when its available — so the ground is effectively charged with heat that is slowly recalled when it gets cold at night. Troy Howard Middle School Garden in Belfast and Salt Farm Flowers in Trenton utilize ground battery systems. University of Minnesota’s Extension’s Deep Winter Greenhouse (DWG) program has the best information on everything from thermal storage of different soil types to spacing of pipes underground.
Natural water-sourced geothermal may be an option forfarmers near bodies of water or those privileged enough to sit on top of one of Maine’s underground aquifers. They might consider an open loop hydronic radiant heat pump system. O’Donal’s Nursery in Gorham is successfully operating such a system to the benefit of their employees and customers.
Bill Giordano is currently serving as education director for the Maine Sustainable Agriculture Society and is an interdisciplinary doctoral fellow at the University of Maine focused on creative rural infrastructure development. He started and ran the vegetable production business Valley of the Stars Farm from 2013 to 2016 which launched as a sister business to Tinder Hearth Bakery in West Brooksville.