Where students and community build relationships through food
By Sonja Heyck-Merlin
Mount Desert Island, Maine: What comes to mind? Maybe it’s catching the sunrise from atop Cadillac Mountain or sea kayaking in a lobster-buoyed bay? Or maybe whale watching, or biking Acadia’s famous carriage trails? Or maybe you roll your eyes, thinking about a $10 ice cream cone or the traffic congestion of Bar Harbor. Afterall, in 2021 Acadia National Park set a record of 4.07 million estimated visits.
Beyond its infamy as a tourist destination and its grandiose second homes, Mount Desert Island has 10,000 full-time residents. These folks — from villages like Otter Creek, Seawall, Town Hill and Bass Harbor — get up each day, maybe walk the dog or get the kids ready for school, and head off to work, helping to keep the year-round economy turning. Anna Davis and David Levinson, farm managers of Beech Hill Farm in Mount Desert village, start the day by rolling up the sides of five high tunnels, managing a harvest crew spread out across 6 acres of organic vegetables, and readying the farmstand.
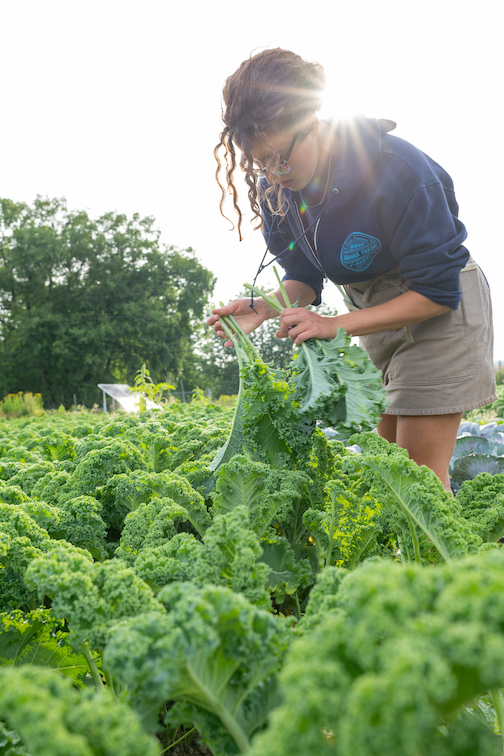
It’s indisputable that all of the people on the island need to eat, whether they’re tourists, summer residents or full-time residents. Davis, Levinson and their crew want to help feed them all, whether it’s through their 100-member CSA (Community Supported Agriculture) or bustling seasonal farmstand, or by providing food to low-income community members with the help of a unique partnership called Share the Harvest.
Davis says, “We’ve been given a tremendous gift, being able to manage this incredible farm in this beautiful location. We want to share this opportunity with our community and see providing locally grown and sustainably produced food as a way to do that.”
The 76-acre Beech Hill Farm is owned by College of the Atlantic (COA). Founded in 1969, COA was the first college in the United States to focus on the relationship between humans and the environment — a relationship the school calls “human ecology,” which is the only major it offers. Each student self-designs a major under the broad human ecology umbrella: It could be environmental law, sustainable business, marine science, educational studies or food systems. Or art, or theater, or gender studies. Really, students can take the human ecology major in any direction as long as they hit COA’s prerequisites and graduation requirements. In 1989, for students Barbarina and Aaron Heyerdahl, that meant buying some land on the “quiet side” of the island and developing a farm business for their senior project. The land was an old chicken farm with some of the best soil on an island better known for its granitic outcroppings and glacial lakes. They named the farm after Beech Mountain, the nearby 839-foot mountain that overlooks Echo Lake.
After graduating from COA, the Heyerdahls farmed until the late 1990s and then decided they wanted to donate Beech Hill Farm to COA. The school accepted the donation with the stipulation that the farm would be managed as a production farm and generate sufficient income to cover operating costs. This model is what attracted farm managers Davis and Levinson, who are also a couple. Davis says, “I was really excited about Beech Hill Farm because it is a college farm that’s run as a production farm. There’s not a lot of subsidy coming in from the college. The bulk of the budget is made from farming.”
One financial boost the farm does get from the college is through the Federal-Work Study (FWS) Program. The FWS Program provides funds for part-time employment to help eligible students finance the costs of postsecondary education. This means the federal government chips in 50% of the wages paid to FWS participants. Each year, Beech Hill Farm employs about 20 FWS students who each work 8 to 12 hours per week. Because of the academic calendar, their work is limited to the spring and fall, but the timing works out well. Davis and Levinson have plenty of help getting seedlings going, prepping ground in the high tunnels (which is all done by hand), and getting a jumpstart on spring transplanting. In the fall, they have extra hands available for harvest-heavy schedules.
The farm also employs a year-round assistant manager and three full-time full-season staff, who are often COA graduates. Additionally, they hire a three-to-four-person field crew for the peak season, four farmstand workers, and two positions in the commercial kitchen. “We received a grant from the Stephen and Tabitha King Foundation to build the kitchen in 2016 in order to increase our capacity to reduce food waste, produce and teach others about value-added foods, and demonstrate strategies for consuming local food year-round. We process and freeze surplus greens and tomatoes to sell to the COA dining hall and also make a variety of products to sell in our farm store including baked goods, soups, salad dressings, tomato sauce and pesto,” says Davis.
In the decades since COA took ownership, this bustling farm has become a space where students, faculty and the public coalesce to experience the relationship between community and food. Davis and Levinson have been managing the farm since 2016. The uniqueness of the mission keeps the couple, who recently became a family of three with the birth of baby Aida, inspired.
The farm has a multitude of goals. First and foremost, it has to pay its way. Beyond that, it strives to provide opportunities for student education and research, and to provide food for COA’s dining facilities. About 5% of the farm’s annual gross sales are to the college kitchen. Last but not least, the farm aims to develop partnerships with organizations to raise awareness and promote action on sustainable agriculture issues and food security on Mount Desert Island and beyond. The primary mechanism for this is the Share the Harvest program, a partner program to the farm that is facilitated by COA. Share the Harvest does all their own fundraising and provides subsidies to food-insecure island residents through a voucher system. Share the Harvest can also kick in to help reduce the cost of a Beech Hill Farm CSA share.
Davis acknowledges these layers can make for complications, like how to find time to help organize a Share the Harvest summer concert fundraiser, but it’s also what she loves. “I find it exciting, and I think it really fuels the farm,” Davis says. “Sometimes we have to prioritize one goal over another. We constantly have to make decisions about which of the goals we’re going to lean into.” She’s found that the more efficient their production is, the easier it to be accessible to the student designing a pollinator garden, the professor heading over with their history of apples class, or to the local gleaning crew cleaning up 500 pounds of misshapen carrots from a field.
Efficiency is dictated, in part, by the confines of the land. The farmstead area with the house, barn, farmstand and wash/pack station sit atop a hill, with fields on the eastern and western slopes. Davis says about 50% of the farm’s beds are 170 feet long, but the rest are a mishmash of lengths, turning crop rotation, tracking production and sizing floating row covers into a bit of a puzzle. They use a zero-turn lawn mower to maintain the grasslands between the puzzle pieces of fields.
In terms of efficiency, their lowest hanging fruit is to control weeds and to improve soil health. Less weeding means more time for other projects, and soil improvements mean healthier plants and higher yields. To help achieve these gains, Davis and Levinson have focused on reducing tillage. The idea is simple: Less tillage means less weed seeds are brought to the surface, and less soil disturbance keeps the microbiota and worms happier.
For Davis and Levinson, reducing tillage meant saying goodbye to their PTO-powered rototiller. About two to three weeks before spring tillage, the crew lays down large silage tarps over winter cover crops. The silage tarps are weighted down by regularly spaced sandbags. They leave the tarps in place for two to three weeks, enough time to break down some of the cover crop residue, and then they run through the gardens with a Yeomans plow. The plow is similar to a chisel plow but with three long straight shanks that cut deeper furrows than a chisel plow. The tractor tires create the pathways while the Yeomans plow slightly raises the soil to shape their beds. Then, they come in with their favorite piece of equipment — a Perfecta field cultivator.
The Perfecta is a three-point-hitch-mounted implement equipped with a series of spring-loaded shanks that penetrate and loosen the top few inches of soil. Following the shanks are a series of rolling harrows that break up clumps and level the soil. “The Perfecta is phenomenal. It has become the centerpiece of our production. We’ve noticed a huge increase in soil organic matter and overall soil health since moving away from the tiller and into the Perfecta,” Davis says.
The Perfecta is the last step of their spring tillage. Then they begin seeding, with a one-row Jang walkalong seeder, or transplanting. Their 5-foot beds allow for three rows of crops like head lettuce, roots, brassicas and herbs. For interrow weeding on these three-row beds, they use a Buddingh belly-mounted basket weeder; it has wire baskets that agitate the spaces between the rows of crops, allowing the crop row to pass between them. Field tomatoes are in two rows, and space-loving cucurbits are transplanted into a single row. Inevitably, there’s still a lot of hand work that gets done: in-row weeding, transplanting without the aid of a ride-behind transplanter and seeding cover crops, for example.
Disposable black plastic mulch is a shoe-in for improving efficiency, but a controversial one. Student workers on the farm keep Davis and Levinson on their toes with their youthful questioning, which often circles back to what role black plastic should play in sustainable agriculture. Davis says, “We get a lot of pushback about black plastic, which is a welcome conversation. We think it’s phenomenal, pushing us every year to say, ‘Is this going to be the year we cut black plastic?’”
To reduce the use of the single-use mulch, they’re experimenting with landscape fabric on winter squash and sweet potatoes. At its full width of 6 feet, they can cover the pathway and shoulders of two beds, leaving an uncovered section in the center of each bed for transplanting into. On the plus side, the landscape fabric is reusable and it’s permeable. On the negative side, it’s more expensive, requires more time to lay out, and allows for copious weeds to grow in the exposed section of soil into which they transplant.
With an eye towards further reducing weeds, they also make use of leaf mulch from local landscapers between beds of cucumber, zucchini and summer squash. Additionally, they’ve started seeding living mulch pathways — an annual ryegrass and clover mix between onions, Solanaceae crops and late-season brassicas. To keep the cover crops short and manageable, they mow them with a walk-behind bush hog. And the goal is always to get the gardens in some kind of cover crop soon after the harvest is complete. Odds are at least one Beech Hill worker has sported the “Don’t Farm Naked” T-shirt; it’s a humorous testament to the importance of cover cropping.
The efficiency push doesn’t end in the field; it extends into the harvest and wash and pack. Currently, the crew harvests on Mondays, Wednesdays and Fridays, freeing up a few days a week to focus on cultivating and transplanting. During the winter of 2023, Davis and Levinson were pushing to complete a farmstand renovation, including enclosing and insulating the structure, and also moving their walk-in coolers closer to the farmstand. By heating the space, they hope to keep the farmstand open longer than six months a year. The extra space will allow them to bring in a greater diversity of Maine-made items such as meat, maple syrup and honey, which they buy and resell.
“We’re going to put heat in so we can stay open later into the season. While the bulk of our sales are in the summer months, there is a really vibrant year-round community on the island. It feels really important to expand our markets into the shoulder season to serve that year-round community and not just focus on the summer population,” Davis says.
With their increased production efficiencies and updated farmstand, the crew at Beech Hill Farm are well positioned to keep feeding the Mount Desert Island community. Whether it’s a private chef who needs some red basil, a local family picking up their CSA share, or a customer using SNAP benefits, Beech Hill Farm strives to feed them all.
About the author: Sonja Heyck-Merlin is a regular feature writer for The MOF&G. She and her family own and operate an organic farm in Charleston, Maine.
This article was published in the summer 2023 issue of The Maine Organic Farmer & Gardener, MOFGA’s quarterly publication.