Twenty Years of Small-Scale No-Till Production in Northern Vermont
By Holli Cederholm
Over the past 20 years, Evan Perkins and Heidi Choate of Small Axe Farm have transformed their quarter-acre homestead garden on a south-facing hilltop in Vermont’s Northeast Kingdom into a 1-acre market garden grossing over $230,000 in annual sales.
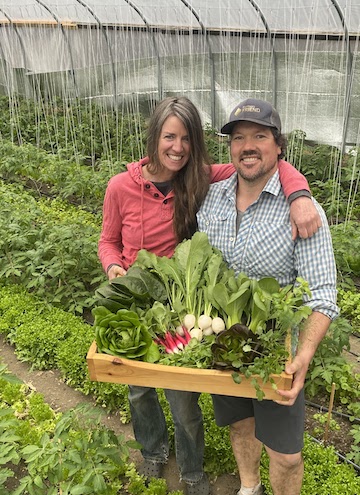
In the beginning, the couple saved $15,000 over three years to secure a land loan in order to purchase 45 mostly wooded acres at 1,500 feet above sea level in rural Barnet, Vermont. “We were able to afford this land because it’s steep. But it’s south-facing, it has great soil, it wasn’t abusively logged before we got it, it has lot of resources on it,” says Perkins.
Early on, they split the cost of a portable sawmill with a friend, each contributing $5,000. This investment paid for itself rather quickly, enabling them to log their land, mill lumber and construct a small cabin and a summer kitchen, which later became the farm’s first wash-pack station. “Building that little tiny structure and living there for four years allowed us the opportunity to have the farm we have now, just being really frugal and being able to put our sweat equity into our land and fields,” says Perkins.
In addition to keeping costs within their means, this human-scaled approach helped them stay true to their desire to live lightly on the land and diminish their reliance on fossil fuels.
Wanting to maintain the woodland as “deep forest habitat,” Perkins and Choate decided not to raze trees to run power lines the 800 feet to the nearest road.
Small Axe Farm remains completely off-grid, relying on the sun to run their household’s electricity needs as well as the farm’s battery-powered tools, irrigation system and a multi-purpose building, which houses an ergonomic wash-pack set-up, a walk-in cooler, a woodshop and an area for growing high-value microgreens in soil flats year-round.
Their first solar system was only 200 watts with one battery — enough to power lights in the cabin — and they later upgraded to 1,000 watts (or 1 kilowatt). “That allowed us to run a washing machine for a greens spinner, to run our well pump for a small period of time if it was sunny,” says Perkins. Their system is now 12 kilowatts. Half of the panels are stationed on homemade moveable racks to track the angle of the sun’s rays throughout the year and the remainder are installed on the roof of their farm building.
The farmers were also reticent to clear forest to create fields. “Only having an acre of our land under production for us is really important because it has allowed us to keep the rest of our land really wild and allow nature to do its thing,” says Perkins.
Their vegetable production area was overgrown pasture from a former dairy when they purchased the property, and it was in tree growth prior to that. Using a rake, a bucket and a hoe, they homesteaded their way into farming, says Perkins. He considers their acre of raised beds “hard-won” from the years of slowly gaining ground by hand, and notes that they still farm among stumps.
It took years until they were ready to farm commercially, and to add employees to the payroll. The turning point, says Perkins, was 2008 when they tacked a strawbale addition onto their cabin. He says they couldn’t run a business out of such a tiny space, “surrounded by squash and onions.” They were able to start paying for labor once they scaled up to three-quarters of an acre.
Perkins attributes their financial viability on such a small scale to a number of things. In addition to slowly and deliberately assembling systems that work for them and the land, they were also thoughtful about matching their production model to their rural community’s needs and the market outlets available to them.
“There wasn’t room in the farmers’ markets, there was not room in stands or CSAs,” says Perkins. “We just pushed into local stores and supermarkets.” Branding was key. Small Axe Farm bartered sweet corn and squash with a local artist, who in turn created a wood cut logo for their business. An idyllic scene of their small cabin hemmed in by sunflowers, celery, cabbage and other vibrant vegetables helped their bagged salad mix stand out at the local co-op. “We built our farm around the fact that people could recognize who were and what we were doing through our label,” says Perkins.
The bulk of their harvest (82%) is grown for direct-to-retail wholesale accounts, mostly local grocery stores and co-ops (72%) with some restaurants (10%) in the mix. They also manage a 17-week Community Supported Agriculture (CSA) program with 50 members and operate an online farm store. While Small Axe Farm produces the full spectrum of vegetables — including a few that aren’t profitable enough to wholesale at their scale, like the winter squash and potatoes they sell retail to CSA customers — they grow a tremendous amount of greens, harvesting over 500 pounds of salad each week. Greens account for 40% of their income, and another 12% comes from microgreens.
An intensive system allows them to reliably produce this volume of salad greens, plus a bounty of other crops, from a single acre. Thanks to fast bed flips — they can harvest a crop and re-plant the space that very same day — their production style translates to higher productivity on the farm. “We can go from one crop, say a crop of salad greens in a bed, and completely turn it over and replant it in an hour — for a 360 bed foot section,” says Perkins. Along with salad greens, they prioritize successions of other “higher-rotation crops,” such as scallions, salad turnips and radishes.
If they have crop residue to deal with, a brush-cutter blade on a weedwhacker clips the plant matter to soil level. Next, a Tillie from Carts & Tools is used to maintain their standardized 30-inch raised beds, throwing soil from their 11-inch pathways onto the growing area, “kind of like a rotary plow would do.” From there, a Tilther from Johnny’s Selected Seeds smooths the bed. Perkins is quick to note that these battery-powered tools disturb the soil surface but do not invert the soil layers, so he still considers the farm’s methods to be no-till.
Once the beds are prepped, which any member of Small Axe’s seasonal crew of five full-time employees is trained to do, they’re ready to either be seeded or transplanted into.
The farmers pass over the bed with a Jang five-row push seeder, its hopper full of a quick-growing crop like salad greens, and then cover it with an old silage tarp from their dairy farming neighbor until germination. Tarping helps to retain the sandy loam’s natural moisture (and limits the need to switch on their solar-powered irrigation pump) while protecting the bare soil from the elements. With a 10-15% grade across the farm, they’re hyper aware of the potential for soil loss, whether over time or in a single weather event. “Through Hurricane Irene and other really intense rainfall events,” Perkins reflects, “we’ve gotten a little bit of erosion here or there, but no major long-term erosion.”
If they’re transplanting a crop, Perkins and Choate will double up on their paper-pot transplanter. Fennel, bok choy, kale, lettuce and broccoli are given a head start to ensure faster, more reliable harvests from the field and to control weeds that could otherwise take hold alongside the longer-season crops if direct seeded. “This tool is a really important part of our farm in terms of our profitability, our strategies for weed management, being able to do a lot of seedlings without a tractor,” says Perkins.
The farm’s labor costs stem from their high-productivity system rather than a need to keep weeds in check. Four out of five days of the work week, their staff is busy harvesting, washing and packing produce for market.
To cut back on harvest labor, they have been using a drill-powered quick cut greens harvester from Farmers Friend since 2012. Perkins says the tool paid for itself within a month. With the cutting labor reduced, they were able to scale up salad greens production significantly and build out additional markets.
“A principle of our farm is to be profitable and make sure our efforts make sense,” says Perkins. To that end, they strategically mix the various types of greens and microgreens they grow to craft different blends — Rainbox Mix, Wellness Blend and Microsalad, to name a few — thereby increasing the number of products they offer on top of plain pea shoots, spinach, baby kale and the like. They can also stretch small salad harvests from their greenhouses during the shoulder seasons by incorporating more abundant microgreens, such as sunflower shoots, into the mix. “It’s been super important to us to be really efficient and to have little go to waste because we have a small production area. These have been really versatile ways just to move everything,” says Perkins.
One effort that doesn’t make sense to them on their scale is growing their own fertility. While the farmers make compost on-farm from manure bedding and rotten round bales from their neighbor’s farm, as well as weed-free pasture grass and leaf mold, they decided against expanding their field acreage in order to produce cover crops. Instead, they import organic fertility, including Pro-Grow (they spread three-quarters of a ton in 2022), feather and grain meals, and compost.
Perkins and Choate are always refining their system to meet their goals. They have plans to cover a quarter of their production space with tunnels. As of fall 2022, they were nearly there. They’re not planning to ramp up production of hot-house tomatoes or cucumbers; rather, they want to plant more greens under cover to ensure more predictable results with unreliable weather. Production under plastic also helps extend their zone 4 growing season through December and allows them to dive back in mid-March, without any auxiliary heating.
Though, the farmers like to scale back their hours in the winter months, prioritizing back-country skiing and long-distance ice skating. “Anybody who has been farming for a while knows that it is pretty hard to do this long term. It’s a stressful thing keeping your body working well, your mental status ok, your marriage or your partnership, or if you’re doing it by yourself, just dealing with yourself every day,” says Perkins. “All those things are challenging.”
Part of their measure of the farm’s success, he continues, is their ability to achieve a balance between their work, their personal lives and their ethos to live simply. For them, it means integrating systems wherever it makes sense to: like using their sod-roofed summer kitchen as a wash station early on, or stuffing a mountain bike into the delivery van — which doubles as their personal vehicle — to catch a ride after dropping produce at market.
Perkins thinks there’s a lot more room for small farms like theirs in the food system. He says, “I want farming to be accessible for people without access to capital resources to get into it.” Perkins hopes that the simple low-cost infrastructure and no capital start-up of their farm can provide inspiration for others who want to farm, but who may not consider farming for themselves as a viable career choice.